My dad always told me to learn as much as I could about the tools I use so I would respect them. He taught me this lesson after he caught me using a hammer, hydraulic jack, cedar siding, and some bungee cords in a nefarious manner that I would rather not share with you.
Dad said that knowing how something is made teaches me its strengths, limitations and, most importantly, never to take it for granted.
I forgot this lesson recently as I cleaned up spilled soda on the work surface of my standing desk. Seeing how the laminate handled the liquid piqued my curiosity: using what material, how are work surfaces manufactured? In this post, I share what I discovered.
Making the Work Surface
The finished work surface that is in front of me passed the eye test. It has a beautiful finish; it is heavy and durable. Comparing the finished product to its primary components creates a disconnect. Why the disconnect? Because when you look at the standing desk, it is hard to imagine that the first step to manufacturing the work surface begins with collecting wood chips and other wood waste.
What is Particle Board?
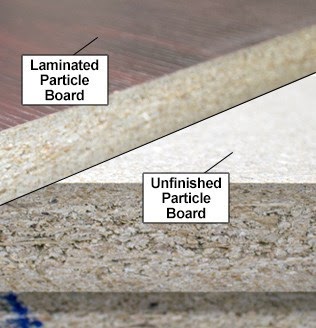
Particle board is a three-layered board with fine particles on the top and bottom surfaces and larger wood flakes in the middle.
Particle board comes in either raw form with a sanded surface or with a surface decorative overlay melamine or laminate. There are three standard grades of particle board available:
- Standard
- Flooring
- Moisture Resistant (MR): much slower response to moisture
Small particles of wood, such as sawdust and small chips, make up particle board. These wood byproducts are glued using a resin and pressed together to form a sheet.
How is Particle Board Made?
The combination of heat and pressure on wood chips, sawdust, sawmill shavings, and resin creates particle board. Wax, wetting agents, release agents, and dyes are part of the resin that makes particle board fireproof, insect proof, and water-resistant.
Mixing the resin, some chemicals, and wood scraps using heat and pressure creates sheets. These sheets are compressed several times forming the tightest bond possible between the wood bits and resin.
This video, produced by Arauco, provides a great example of manufacturing particle board and its laminations.
Particle board is a cost-effective material that is easy to work with and light. Moisture and humidity are the two biggest disadvantages of using particle board. The board expands and contracts as the level of moisture around it change.
Standing Desk Laminations
The two most common types of laminations for particle board are thermally fused laminate (TFL) and high-pressure laminate (HPL).
Thermally Fused Laminate
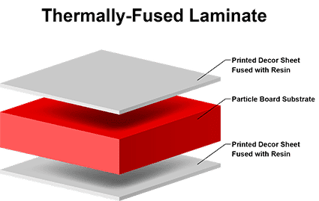
Laminating a particle board using the TFL process takes one step: fusing a sheet of decorative paper that is suffused with resin directly to the particle board.
Exposing the particle board to 350 ºF heat and pressures exceeding 400 pounds per square inch activates the resin that saturates the decorative paper, which creates a crosslinked bond with the particle board.
Crosslinking is the process of chemically joining two or more molecules by a covalent bond.
High Pressure Laminate

Laminating a substrate using the HPL method takes a few more steps.
The laminate clippings of three layers:
- Resin-impregnated Kraft paper
- Decorative paper
- Clear melamine overlay
The layers moved down the production line and heated to 350 ºF heat and pressures exceeding 1,000 pounds per square inch. The resulting material is laminate. The laminate is attached to the particle board with glue.
Edge Banding's Edge
Rather than being overlooked, edge banding became ubiquitous and a critical ingredient for quality work surfaces for hiding the manufactured wood underneath
Edge Banding
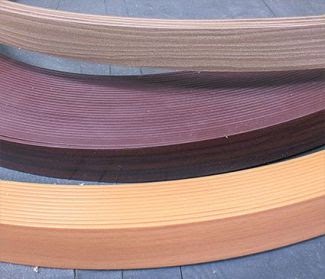
Polypropylene Edge Banding
The sides of any engineered wood are at best, rough. An unfinished, unmatching edge ruins the world’s most attractive decorative laminate. Edge banding is applied to cover the exposed sides, which gives the standing desk the appearance of a solid piece of wood.
The edging of particle board is carried out to match the surface treatment of the substrate. There is a variety of material used for edge banding:
- PVC: the most popular material used on pressure laminate
- Polypropylene
- ABS
- Acrylic
- Melamine
- Wood
- Wood veneer
Hot-Melt Glue Edgebanding
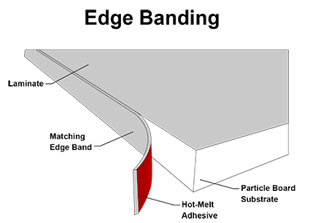
An edgebander is the machine applying the edge banding to the substrate automatically using hot-melt glue.
The hot-melt adhesives are water or solvent-based and contain one or a combination of the following:
- Hot air
- Ethylene vinyl acetate (EVA)
- Polyurethane (PUR)
- Polyamide (PA)
- Amorphous poly alpha olefin (APOA)
- Polyolefin (PO)
Edgebanding Premill
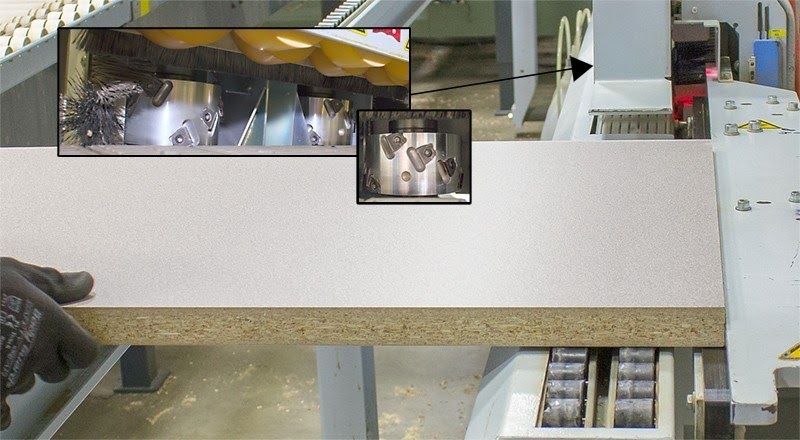
RightAngle’s 4EVERedge Premilling for a Standing Desk
As it leaves the edgebander, the leading and trailing edges are automatically sliced. The top and bottom sides are trimmed, so the edging material sets flush to the substrate. Any surplus edging is then scrapped and the edgebander buffs the finished edge.
Hot-melt glue edgebanding is the most popular method companies use to add an edge to a substrate material. The hot-melt glue is applied using a glue-pot or cartridges.
Hot Air Edgebanding
One of the newest methods to add edging material to a substrate is to use hot air. Hot air edgebanding features higher heat and moisture resistance compared to hot-melt glue.
Instead of applying hot-melt glue to the edge material, hot air edgebanding equipment activates a color-matched functional layer on the reverse side of the edgeband and welds it to the board. The result is obvious, especially when compared to the traditional hot-melt glue method, there is a zero edge. The photo above is an example of the two ways of edge banding on a single piece of substrate. The picture to the right illustrates the difference.
Features
- Creates a stunning high-end look using the latest technology
- Allows for a monolithic panel at a much lower price than solid or painted
- Enhancing leading industry trends (high gloss and textured panels) with no framing effect
- No glue joint to collect dirt, chip away or yellow over time
- Creates a bond equal to or greater than PUR (no delamination)
- Extremely heat and moisture resistant bond
RightAngle Product’s 4EVERedge
When first introduced, Bill Knighton became an early advocate of hot air edgebanding. Despite the higher expenses related to the hot air method, Knighton featured the 4EVERedge™ as a standard edge for all RightAngle products. For him, the decision was easy for the following reasons:
- Virtually invisible joins with state-of-the-art hot air technology for straight line work surfaces.
- Seam-free edge offers increased aesthetic appeal and is resistant to solvents, dirt, heat, and moisture.
- Features include precision edge for an optimum join quality with maximum adhesion.
- Edge material is fully recyclable, halogen-free, odorless and is a very neutral polypropylene material.
- Higher UV resistance to fading.
The 4EVERedge offers a limited lifetime warranty:
If 4EVERedge (2mm non-PVC edging) covered by this warranty delaminates due to a manufacturing defect, we will repair the product, without charge, or replace it, at our discretion. Only original, unaltered and unmodified materials and workmanship are covered by this policy. This warranty does not cover damage caused by accident, improper care, negligence, normal wear, and tear, or the natural breakdown of colors and materials over extended time and use. Costs incurred due to product replacement such as installation, labor charges or transportation are not covered under this warranty. Product service life is 15 years.
In Sum
There are several varieties of engineered wood, each with their pros and cons. For the standing desk industry, particle board is the standard type of substrate because of its ability to be cut to shape and trimmed.
Completing the process is the application of edging material. Similar to engineered wood, the diversity of edging material, and how it is adhered to the substrate varies—depending on the final product.
Remember, don’t take the work surface of your adjustable height desk for granted. The whole sit to stand unit represents a substantial investment that deserves respect.
COMMENTS